Ein komplettes Angebot an Mast und Takelage
Bei VMG Soromap stehen die Initialen für Voile Mât et Rigment (Segel, Mast und Takelage). Sie verdeutlichen die Entscheidung des in Rochefort ansässigen Unternehmens, alle Produkte anzubieten, die für den Bau eines Segelschiffs erforderlich sind, wobei jedes Produkt ein bestimmtes Know-how erfordert. Wir beschäftigen uns hier mit dem Produktionsleiter Nicolas Lecuona mit der Herstellung von Masten, Spieren und Takelagen. 9 Mitarbeiter arbeiten hier täglich an der Herstellung von über 300 Masten pro Jahr und hunderten Kilometern Takelagenkabel.
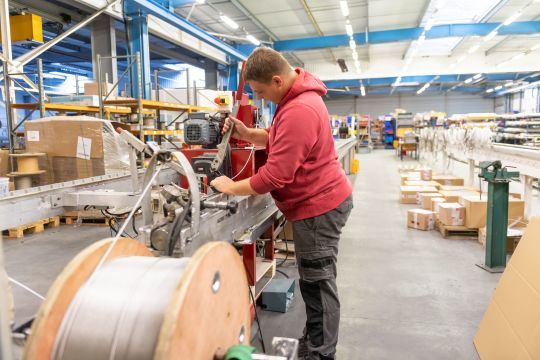
Rückverfolgung von Kabeln und Rigging-Zubehör
Im Rahmen seines Rigging-Geschäfts beginnt die Expertise von VMG Soromap bereits bei der Beschaffung. Das Unternehmen stellt die Qualität der Kabel sicher, die es von koreanischen Lieferanten für einsträngige oder flexible Edelstahlseile für das stehende Rigg oder von anderen asiatischen Lieferanten für die Spinnakerei kauft. Alle Verbindungselemente und Endstücke werden intern entworfen. Die Schmiedeteile (Ösen-/Kugelendstücke) und bearbeiteten Teile (einfache Gewindeendstücke/Schlitzendstücke) werden in Tunesien innerhalb der Soromap-Gruppe bei einem Schwesterunternehmen hergestellt. "Wir haben eine Rückverfolgbarkeit über alle eingekauften Rohstoffe und Komponenten" erklärt Nicolas Lecuona.
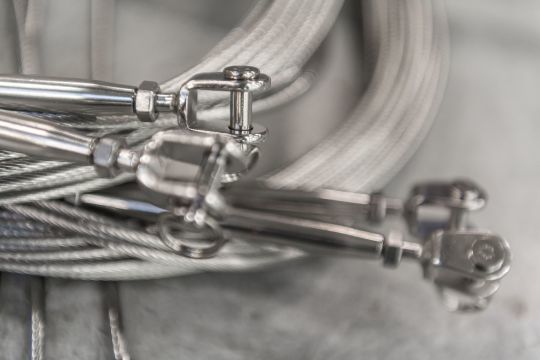
Maßgeschneiderte Takelagen für jedes Schiff
Die Herstellung der Rigg-Elemente erfolgt entweder anhand des vorhandenen Riggs, das der Kunde bei identischen Änderungen einsendet, oder nach Plan anhand der von einem Vertriebsmitarbeiter erstellten und vom internen Büro überprüften Kadettenaufstellung oder der Pläne des neuen Bootes. Professionellen Takelern steht ein Konfigurator zur Verfügung, mit dem sie ihre Bestellungen automatisch generieren können.
"Anschließend wird anhand der Kundenaufträge ein interner Fertigungsauftrag erstellt. Er enthält eine Tafel mit der Beschreibung des Riggs mit seinen Elementen, Vorstag, Wanten, Galgen usw., sowie eine Liste der Teile, die aus dem Lager zu entnehmen sind, und schließlich eine Konformitätsbescheinigung" führt der Produktionsleiter detailliert aus.
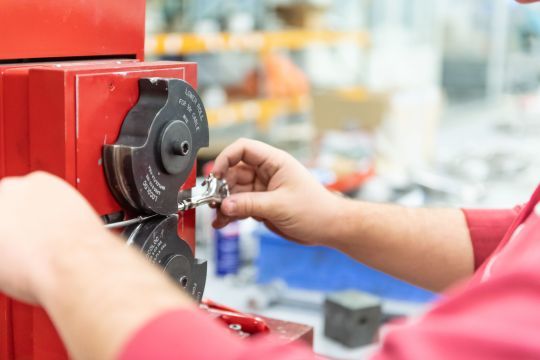
Der Bediener schneidet die Kabel auf die richtige Länge zu und crimpt sie dann nach dem internen Verfahren. Jedes Kabel durchläuft dann den Zugprüfstand, um die Crimpqualität zu bestätigen, wobei es bis auf 10-15 % der Bruchlast belastet wird. Er überprüft die Länge des Kabels. "Der Mitarbeiter unterschreibt dann die Konformitätsbescheinigung, bevor sie an den Kunden geschickt wird" betont Nicolas Lecuona.
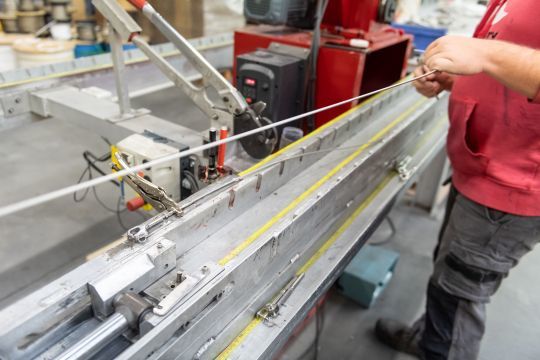
Das Produkt wird dann von der Logistikabteilung von VMG Soromap mit einer dem Zielort angepassten Verpackung in die ganze Welt versandt.
Exklusive Mastprofile
Die Masten des Herstellers werden in der Entwicklungsabteilung von VMG Soromap entworfen und sind ausschließlich für den Hersteller bestimmt. Er verfügt über eigene Produktionsstätten, die es ihm ermöglichen, stranggepresste Aluminiumprofile nach seinen Wünschen in Europa herzustellen. "Sie kommen bereits eloxiert bei uns an, um eine Behandlung in Industriequalität zu haben. Wir lagern sie dann in einem speziellen Bereich, wobei wir sie mit Gurten transportieren, um sie nicht zu beschädigen." erklärt der Leiter.
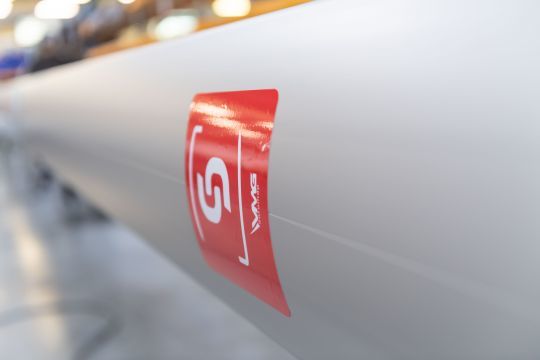
Die geschmiedeten Produkte werden in der tunesischen Niederlassung von Soromap hergestellt, während die Edelstahl-Mikrofusionselemente in Formen, die Eigentum von VMG Soromap sind, in Lohnarbeit hergestellt werden.
Bearbeitung und Ausrüstung von Masten
Dann kann die Produktion beginnen, nachdem der Mast zunächst einer Sichtprüfung und dann einer geometrischen Prüfung unterzogen wurde. "Wir prüfen die Geradheit, die Verdrehung... direkt auf dem Bearbeitungszentrum, das ein präziser Marmor ist. Wir haben zwei Bearbeitungszentren: ein 18,5 Meter langes 4-achsiges und ein 23 Meter langes 5-achsiges" sagt der Mastspezialist.
Nachdem der Mast bearbeitet wurde, wird er von Hand entfettet und entgratet. "So kann man die Bearbeitungen überprüfen" gibt der Verantwortliche an.
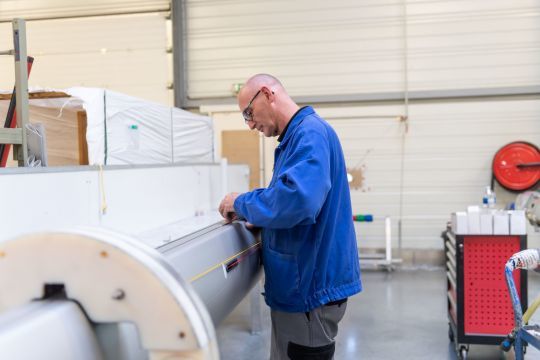
Die Arbeiter ziehen dann die Iro-Rohre, die Kabelschächte, durch. Parallel dazu bereitet eine Person im Lager die gesamte Beschlagsausrüstung vor, die am Mast montiert werden soll. "Die Montage am Mast dauert 4 bis 12 Stunden, je nach Komplexität, z. B. wenn es einen Sleeve für den Exportversand gibt. Anschließend kontrolliert der Werkstattleiter den Mast mit dem Dekameter, überprüft, ob die Teile an der richtigen Stelle sind, ob die Steppung an der richtigen Stelle erfolgt ist, ob es keine Kratzer oder Anomalien gibt und unterschreibt den Arbeitsauftrag, ebenso wie der Arbeiter" schließt Nicolas Lecuona.
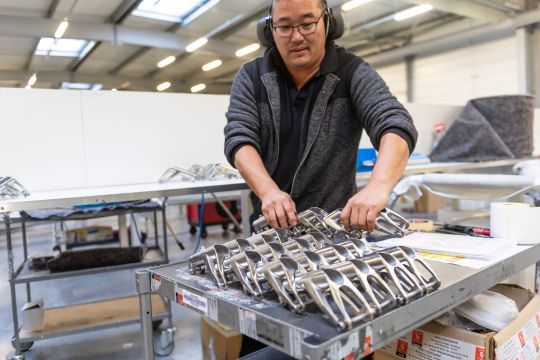
Sich an den Kunden anpassen
Ob es um die Endverarbeitung oder die Versandbedingungen geht, VMG Soromap passt sich dem Kunden an.
Eine 25 m lange Lackierkabine ermöglicht es, mit Hilfe von Soromap SPV, der Tochtergesellschaft, die ihre eigenen Produkte herstellt und formuliert, eine Lackierung oder eine Lackfarbe nach Wahl anzubieten. Die WIG-Kesselbauwerkstatt kümmert sich um die Herstellung von Schrumpfungen an der Mastspitze für Segler, die auf der Suche nach Leichtigkeit in den Tops sind.
Ringelschläuche schützen die Masten, die für den großen Export verschickt werden.
Mit seinem erfahrenen Team erfüllt VMG Soromap die Wünsche seiner Kunden, die sich auf sein Kerngeschäft, Segelboote von 20 bis 60 Fuß, konzentrieren.